95%的材料浪費能想象麽?火箭外殼加工的時候,通常情況下有高達 95% 的材料在加工中浪費了。南非人埃隆·馬斯克覺得這太不可思議了,他要求大幅改進工藝,並將其套用到了Model Y的制造上。
1. 驚人的浪費
在將航天工程推向極限的過程中,馬一龍同誌並不滿足於采用一些業內通用多年的做法,而是對其進行了大刀闊斧或者異想天開的改革,讓它在功能不變的情況下,變得既便宜又易於翻新。比如說火箭箭體的處理上,就把這個想法用到了極致。
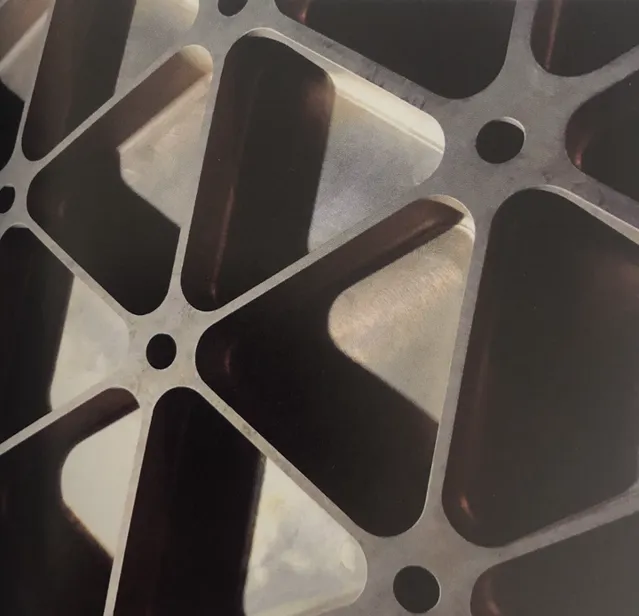
上面這種等網格結構,在許多運載火箭和衛星的殼體設計中經常會見到。我們知道,火箭的輕量化決定了其運載能力,是研發新型火箭時必不可少的一環。在早期的火箭研發中,為了讓火箭足夠輕,會把火箭死重中的圓柱形外殼做得很薄,就像一個可樂鋁罐,一不小心就會被壓扁(殼體屈曲應力不足)。比如下面這枚阿特拉斯火箭,殼過薄了導致其在自身重量下倒塌了。
那怎麽才能在保證強度的同時減輕火箭品質呢?上世紀太空競賽的那個年代,有限的技術和制造水平,加上沒有高效的電腦的加持,只能先透過增加大量不必要的重量來換發射的穩定性。 [1]
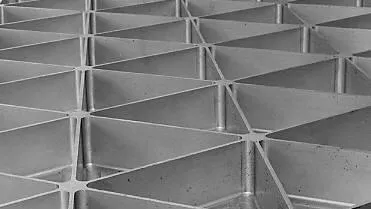
後來透過不斷的實踐,終於摸索出了『等網格』這種能提高材料的強度與重量比(比強度)的消減品質方法,讓火箭變得比以前更輕。這突然讓我聯想到了英格蘭古老的萊斯特城中的一處15世紀建築裏的拱頂:
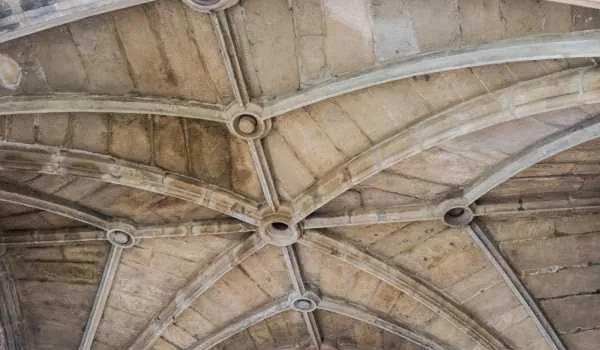
(好想再引申寫一下哥特。。算了,此處省略一萬字)
理論上NC銑床可以把鋁板變薄到只有1公釐 [2] 。聯合發射聯盟(SpaceX的競爭對手之一)的兩員主將:擎天神和三角洲火箭就是采用的這種等格設計。
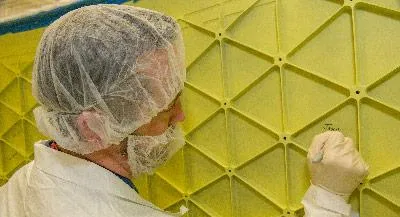
具體怎麽實作的呢?說來也簡單,就是在圓柱型的金屬厚內壁上,打磨出一個挨一個的幾英寸邊長的三角形。最早是人工一個個銑出來(人工費相當貴),現在一般用數控機床。
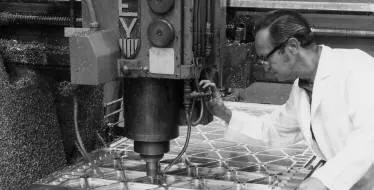
每個三角形雖小,但數以萬計的三角形網格,就會明顯消減火箭的重量的同時,還能最低限度的保證火箭結構穩定。它能夠承受驚人的壓縮和彎曲載荷,但是缺點也很明顯,那就是制造成本非常昂貴。磨掉金屬廢料的品質相當驚人,最高能占到原金屬品質的95%,這個工序即耗時,又耗錢。
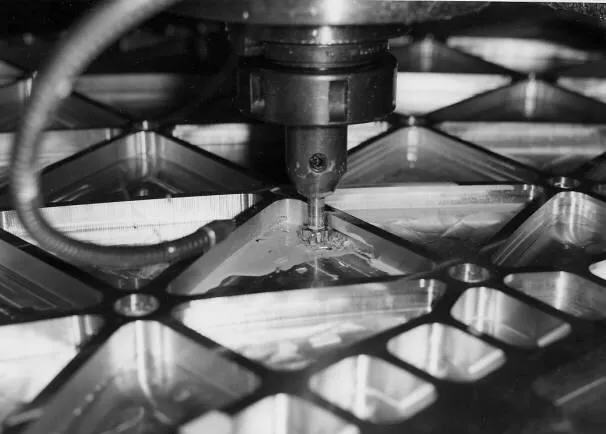
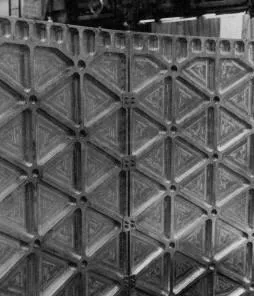
火箭最初因為是為了保家衛國而設計的(擎天神和三角洲火箭都是發射核飛彈起家的),要求是如此之高,以至於在設計標準中,成本並不是最優先考慮的一項。無論加工多麽困難和昂貴,只要能夠完成任務,就可能會被選中。然而,隨著太空商業化的推進和每年發射次數的增長,私人公司的火箭發射不得不考慮成本問題。因此,第一性原理思想指導下的SpaceX公司,並沒有延續使用這種典型的等網格結構,而是使用另外一種技術來達到類似的效果。嗯,商人連材料加工的剩余價值都要榨幹。
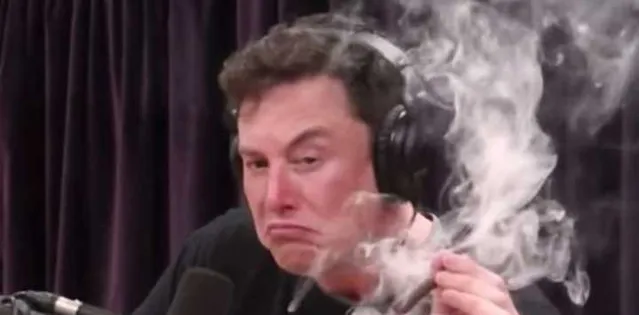
2.從減法到加法
第一性原理告訴我們,要看透事物的本質, 回歸到事物本源去思考解決方案 。
「 我們絕大多數時候都是類推地思考問題,也就是模仿別人做的事情並加以微幅更改。但當你想要做一些新的東西時,必須要運用第一性原理來思考 。」---馬一龍在加強火箭壁比強度這件事上,為什麽不直接把網狀結構直接做出來然後焊在殼上呢?
因為傳統的焊接技術達不到要求。就拿氬弧焊來說,不論是引弧的電流過大引發的燒穿、還是焊接導致的膨脹收縮變形、氧化等缺陷,都無法在極薄材料上滿足機械效能要求。其它技術比如電子束焊技術倒是完全可以做到,焊接變形小,精確度也更高,但要求在真空環境作業,成本也是下不來。
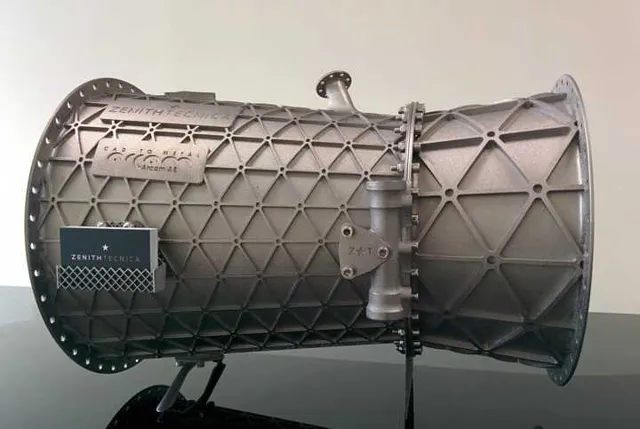
馬一龍最終采用的是 攪拌摩擦焊接技術( 這個技術是波音公司最早套用在火箭制造領域的)。從2008年獵鷹9號(世界上第一個全面套用高強2195鋁鋰合金的火箭)第一級貯箱箱體焊接開始,SpaceX就一直在一斷使用並改進這個工藝。這是一種革命性的新技術。簡單的說,就是用一個高速旋轉的攪拌頭使勁壓在待焊截縫上,透過大力出神奇讓兩塊材料像奶油一樣擠壓攪拌到一起,形成致密的你中有我、我中有你的固相連線。這種方法材料及能源耗費更少,成本效益更高,材料可以更薄(小於1 mm) [3] ,更重要的是,焊接過程既不需要瓦斯保護,也不會產生有毒瓦斯,因此對工人和環境都更安全(不過以後是不是用機器人就不好說了)。除此之外,速度快、易於自動化、還能焊接不同材料(例如塑膠與合金),焊縫更牢、更滑、更輕量,抗疲勞性和抗拉強度更高,制成的貯箱扭曲變形更小 [4] ,焊後材料效能可與未焊材料效能相媲美 [5] 。優點簡直多多的,連密封核廢料時都會用到它。
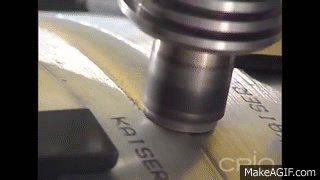
這種加工方法的改進,可以讓加工效率提高一倍,而成本會降低一半。
馬一龍認識到, 攪拌摩擦焊 這個技術省時高效相當完美,更少的零件和更少的組裝時間意味著更低的成本。本著物盡其用的原則,已經給Model Y配上了。對於一體化車身的Model Y來說,這個技術可以維持車體鋁件的強度,確保各部件結合處的可靠性的同時,零部件也不會因為焊接而變脆,沒有火花星,也沒有難聞又有毒的氣味 [6] 。另外,焊接時部件的非焊接部份不會承受不必要的應力,對焊縫造成的殘余應力也小於標準的熔焊,從而可以延長其壽命,提升電動車熱管理的有效性 [7] 。
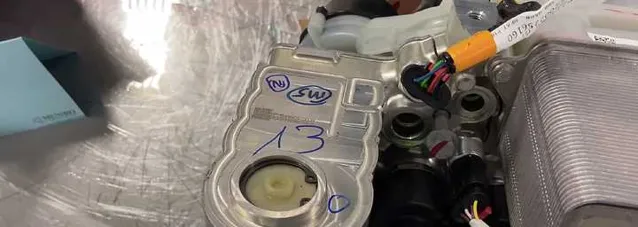
3.管中窺豹
上面講到的工藝只是火箭制造控制成本的很小的一個細節,很多大廠都在用,並不是馬一龍一家獨享的技術。但千千萬萬個微創新合在一起,就能從量變到質變,大幅降低成本。比如獵鷹9號火箭底部的九個發動機陣列載荷架,之前都是用焊接工藝,現在反而全改成用螺栓連線,因為這樣可以讓翻新變得更容易、更快,變相的降低了再利用的成本。
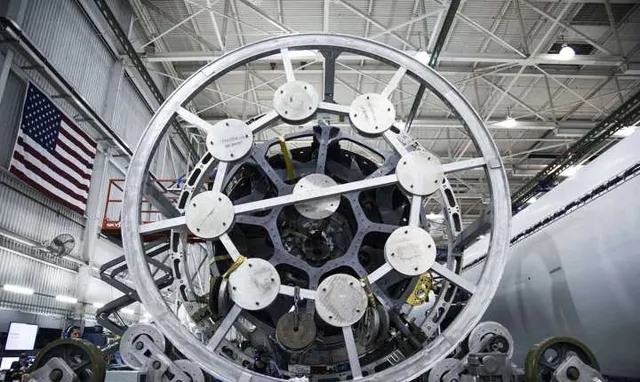
另外就是大家都知道的關於不銹鋼的使用。以前用碳纖維復合材料時,原材料成本大概是每千克135美元,廢品率約35%,最終部件的實際材料成本為每千克200美元左右。SpaceX的理想是讓發射火箭和開飛機一樣便宜,太貴的材料是不行的,那就直接用不銹鋼吧,雖然密度高,但導熱系數只有傳統鋁鋰合金的四分之一(有利於低溫燃料的保溫,將箱體結構和隔熱板部件整合化),降落火星時還能降低對熱遮蔽的要求,最關鍵的是采購價僅為每公斤3美元,成本降低了近兩個數量級。
再說一個大家都不敢相信的。如果你有機會去加州霍桑的SpaceX工廠參觀,記得去總部一樓的咖啡館點杯咖啡,然後看一下就在旁邊的助推器組裝大廳。如果正好是在組裝燃料箱的話,你有機會能看到有工人在用研磨機粗糙地打磨燃料箱罐體外表面,磨完的表面相當醜陋和不高科技。和業內普遍都打磨火箭外殼相比,打磨燃料箱成本更低,耗時更短,也就是用更少的投入獲得更大的報酬,典型的商人思維。
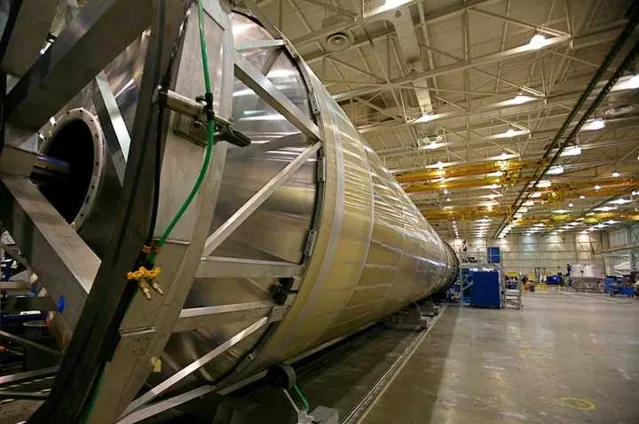
但想要真正的大幅成本縮減,必須將火箭發射商業化,也就是走飛機營運的路:沒有誰會坐一架飛機從紐約飛到上海後把飛機扔到海裏的。火箭、太空艙、整流罩的重復利用,可以省掉火箭發射最花錢的部份———制造。獵鷹9號的最終目標是將發射成本從每公斤5000美元降到每公斤200美元(請自行代入體重)。獵鷹9號將來的每次發射費用也就幾百萬美元(現在是6000萬美元),也就是上海市區幾套房子的價格罷了。因為火箭和相關硬體占了成本中的絕大部份,燃料成本只有20萬美元(其它還有檢查和翻新所需的時間成本)。
4.理念
和蘇聯人「能用就湊合用到底」的航天理念不同,SpaceX遵循著「不斷尋找更好的替代方案」的理念,如果一個改進方案能提供更卓越可靠的效能、或者更低的成本,馬一龍會毫不猶豫地實施徹底的設計升級。他並不把火箭發射當成科研計畫來看,而是一門生意,所以工廠註重的是批次生產,而不是生產最高精尖的裝置。所有的東西足夠好用,但是絕對不會超過這個標準(相信如果你開過特斯拉的Model 3,你就更理解我在說什麽了)。
與其說SpaceX是下一個蘋果,不如說它更像17世紀的東印度貿易公司。
完美不是它的代名詞,資本報酬才是。
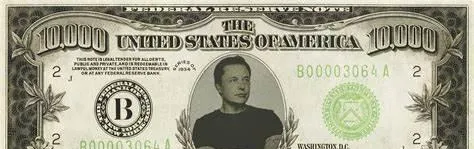
一更
有人問如何將格柵網狀的金屬透過攪拌摩擦焊技術焊到殼體上?上面那個演示只有平面連線嘛。
嗯,準確的說,這是商業機密,因為spaceX在TWI公司(發明攪拌摩擦焊的公司)技術基礎上,開發了一套自己的技術。但如果你有機會去到工廠現場參觀的話,你會發現基本的實作原理還是TWI初始的那一套。我截了一個內部宣傳視訊,看一下就明白了。
不過SpaceX用攪拌摩擦焊最多的,還是用在大鋁罐子上的,那個就相對容易多了。
另外,再多說一點,關於「加法」的概念。仔細看下面這個DED直接能量沈積成形視訊,也許你對等格加工中的「加法」會有新的認識。
客官,都看到這兒了,點我頭像加個關註唄! 我保證會寫很多無用的知識給你看的!
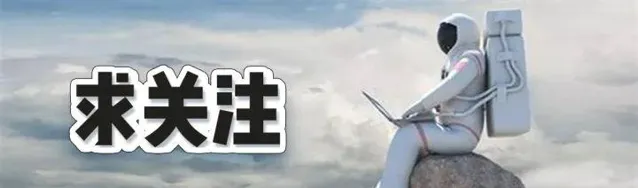
參考
- ^http://www.nasa.gov/topics/technology/features/buckling2.html
- ^https://archive.is/saWnK#
- ^ M. Ashby, 「Material and process charts」, The CES EduPack Resource Booklet 2, Cambridge University, Granta Design, 2010.
- ^ T. D. Kim, 「Fabrication and testing of composite isogrid stiffened cylinder」, Composite Structures, Vol. 45(1), p. 1 – 6, 1999.
- ^https://www.energy.gov/sites/prod/files/2015/11/f27/Friction stir additive manufacturing-DOE-AMM-9-29-15.pdf
- ^https://www.comsol.com/blogs/examining-heat-transfer-in-a-friction-stir-welding-process/
- ^http://www.teslarati.com