目前很多企業在數位化轉型過程中,上了ERP、MES、WMS等系統,但真正能夠借助這些系統實作企業流程最佳化、業務整合、資源最佳化配置的卻不是很多。這是為什麽呢?
數位化轉型,的確需要先資訊化,而資訊化的實作離不開ERP、MES、PLM等系統。但要系統發揮作用,除了部署這些軟體之外,還需要理解和遵循系統背後的管理邏輯、流程最佳化等過程,需要對原有不合理的流程進行梳理、最佳化和再造。這就需要精益技術對業務全過程資訊流和實物流進行精益化和標準化改善,這是前提,然後再透過智慧制造進行資訊化和數位化提升,才能事半功倍。
金屬制品行業作為國民經濟裏面一個重要行業,和我們工作、生活息息相關,其數位化轉型具有代表性。下面就以金屬制品企業為例,探究精益和智慧制造如何結合,實作企業數位化轉型。
1 ► 金屬制品企業現況
金屬制品企業,指的是對相關金屬材料構成的產品進行生產、加工、制造、銷售的企業。涉及下料、切割、車/銑/鉆、沖壓、折彎、焊接、噴塗、部份還有裝配等工藝,機加工序占大頭。原料、在制品和成品數量一般都比較大,且涉及眾多金屬原材料、機器裝置、模治具等。大部份金屬制品企業在現場環境、作業效率、過程狀態、產品品質和管控等方面都存在不少問題,下面從人、機、料、法、環五方面分別闡述。
人方面
①雖然現場有眾多機器裝置,但人機配合和過程管控、資訊傳遞,大部份還是靠人控制;
②人機配合欠缺,操作和搬運效率差;
③一般為計件制,因存在跨期訂單和不同批次原料,人力和生產成本核算準確較困難;
機方面
①裝置種類多,大部份較老舊,維護保養不到位,狀態無法保證,經常出現停機異常;
②裝置利用率差,OEE存在較大提升空間;
③裝置和模治具管理粗放,導致狀態不穩定,產品品質無法保證;
料方面
①眾多金屬原料,體積大、品質重,缺乏有效存放工具和方法;
②生產訂單安排不夠合理,需求變更多,導致在制品數量眾多,容易積壓形成呆滯或報廢;
③過程產生眾多邊角料,缺乏有效利用機制,導致原料成本高;
法方面
①現場手工作業多,效率差,資訊傳遞慢,容易遺失;
②過程管控缺乏有效機制,狀態無法即時感知;
③原料體積一般較大,機加工藝多,過程數量較多,質檢作業困難,效率差;
環方面
①現場臟、亂、差,倉庫和生產車間狀態混亂;
②現場環境差,人員體驗不好,人員離職率高,招工難;
③現場裝置、訂單、生產狀態無法及時、有效獲取,管理人員無法及時獲悉並處理;
針對以上問題,如何 透過精益+智慧制造 ,進行最佳化提升,實作數位化轉型升級呢?
2 ► 智造資訊流改善
以上金屬制品企業的問題,歸納總結是作業模式和流程不合理,資訊缺失和未有效傳遞與利用;物料、機器裝置、人員等資源缺乏最佳化管控、生產過程管理粗放等,需要依據企業戰略和業務需求,結合銷售、采購、計劃、生產、物流等業務流程,進行業務資訊流和產品實物流的全方位最佳化改善。在基礎流程最佳化改善後,建立標準化和規範化管控,再匯入PLM、ERP、MES等資訊系統進行最佳化提升,後進行數位化營運和智慧化提升。
針對業務資訊流,我們逐個最佳化改善。
(1)要最佳化業務流程,首先需要對產品BOM、工藝路線和工藝參數等進行最佳化配置。只有詳細和規範的BOM,並實作模組化和通用性設定,並有對應詳盡的工藝路線和工藝參數,才能針對客戶個人化和客製化需求,快速配置,並按計劃高效投產、完成交付。
優秀的產品如金蝶雲·星空(簡稱星空),ERP+PLM+MES一體化,針對產品結構,進行模組化設定,快速組合依需構建設計BOM、產品BOM到制造BOM,並實作系統間數據共享。透過工程數據模組,進行產品工藝路線維護、工藝參數和標準工時設定,從源頭詳細定義和最佳化產品構成、資源安排,實作業務資訊順暢高效執行。
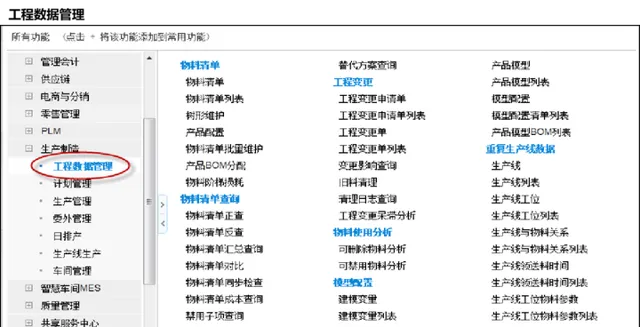
(2)要滿足精細化管控和高效順暢生產需求,需要掌握行業特性的物料資訊,需要先進行基礎資訊詳細定義和系統管控,如厚度、寬度、長度、材質、表面、產地、卷號、圖號、數量等。星空除了能詳細定義和管理以上參數之外,還支持所有單據和業務場景體現行業特性資料。
(3)要想生產過程順暢和確保資源合理利用,需要構建產供銷協同計劃體系。透過打造多級計劃,進行計劃的準確制定,資源(物料、人力、裝置、模治具等)計算和合理安排,實作按需拉式作業。
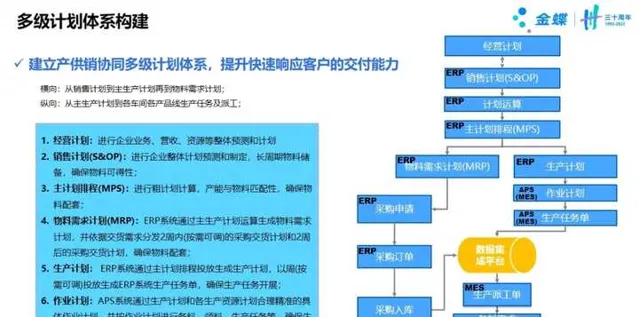
(4)要實作過程精細管控,需要透過MES對作業檔、工藝標準建立防呆防錯套用。透過MES和ERP打通,實作BOM、產品名稱、圖號、ESOP、訂單、狀態等數據的共享和運用。並和套料軟體快速整合,實作圖紙設計、程式、訂單資訊的打通,高效流轉。
(5)要想建立高效作業模式和追溯體系,需要建立各資源資訊采集和運用體系。透過條碼管理,對物料、半成品、成品、裝置、模治具、庫位、單據等資源要素建立條碼的全方位套用。並透過掃碼作業,實作批次或單件序列號管控。並透過ERP和MES系統,形成追溯體系,實作精細化管理和效率提升。
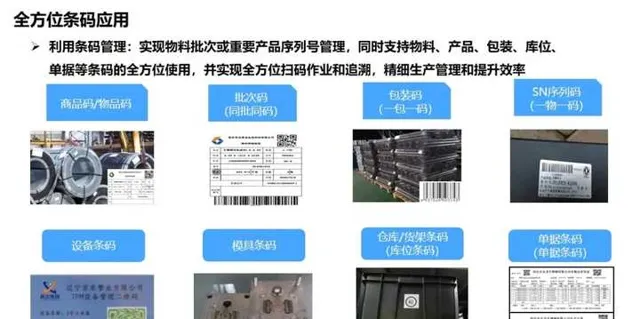
(6)要想提升物料利用率,減少邊角料產生;對於產生的邊角料,要提升回收利用率,需要強大的排版下料和回收利用能力。星空透過智慧排版下料,依據產品需求和物料規格,實作智慧匹配和最大化排版設計,實作金屬材料的高效利用。透過余料最大可用矩形面積記錄,在物料需求時自動計算余料是否匹配並進行優先使用,實作邊角料的最大化利用。
(7)要提升過程作業效率和精細過程管理,在業務流程梳理最佳化後,透過MES深化套用,實作生產過程電子化、任務移動化下達、開工、報工、入庫、品質管控、質檢、審批等精細化管理作業。

(8)要確保裝置和模具狀態,提升OEE和產品生產品質。可匯入裝置和模具管理,實作裝置和模具從采購、驗收轉固、日常維護保養、點巡檢、快速維修、備品備件、出入庫管理、狀態變動等全生命周期的精細化管控,實作裝置和模具要時能有,有時能用,用時能穩,提升品質狀態和OEE。
3 ► 精益實物流改善
數位化轉型,除了資訊流程最佳化改善之外,需要結合戰略和業務需求,進行生產方式、節拍、作業、物流、布局等實物流程改善。在基礎流程最佳化改善後,建立標準化和規範化作業體系,再輔助PLM、ERP、MES等資訊系統進行升級最佳化,實物流動和業務資訊同步改善,後進行數位化營運和智慧化提升,方能取得整體最佳效果。
實物流程的最佳化改善,需要精益技術體系進行最佳化配置。針對上述金屬制品企業的問題,企業需要一個高效、合理的生產運作體系,首先需要:
(1)結合未來戰略和業務發展,對產品系列進行最佳化配置,需要進行PQ分析。基於未來業務需求,透過PQ分析,能將未來業務規劃落實到產品和資源支持上來,這是構建生產運作模式的基礎。如下圖展示的是凈飲水行業客戶,要實作年產500萬台的目標,結合市場需求,需要具體到各產品需求和對應年份時間。
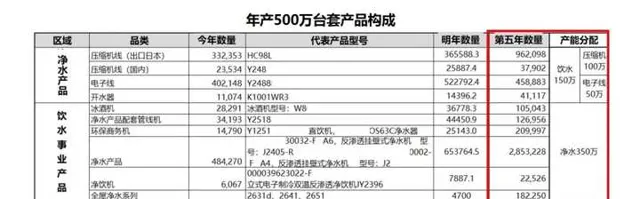
(2)對產品BOM和PFEP數據進行收集並分析,結合未來產能需求制定企業整體生產節拍和物流配送效率。這是生產運作模式的具體實施措施。
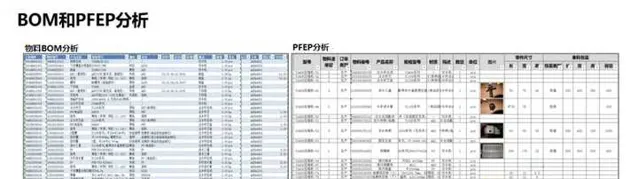
(3)結合未來業務需求、進行產能拆解,評估配套資源(人力、裝置、場地、廠房等)。只有合適和足夠的資源支持,戰略和業務規劃才能落地,否則都是空談。這是生產運作模式能順暢實施的有力保障。
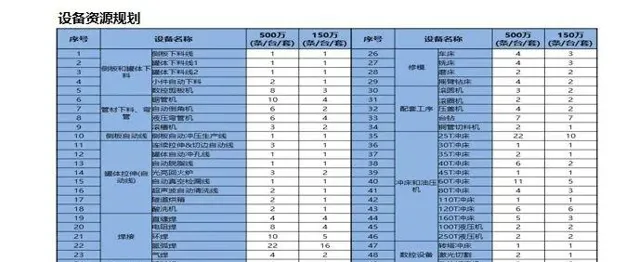
(4)依據計算的配套資源,進行整體布局(含園區、樓棟、車間和線體等)最佳化設計,確保具體資源落地和整體系統最優。這是生產運作模式在場地和空間的直接表現形式。
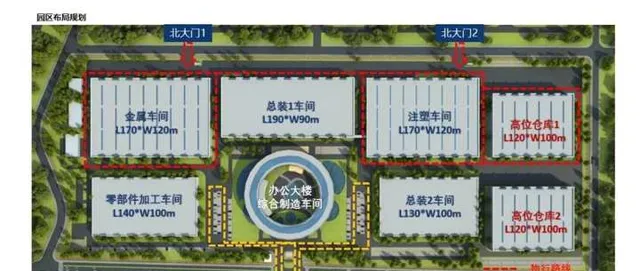
(5)結合布局設計,進行整體作業流程和物流配送最佳化設計,實作生產體系落地。這是生產運作模式的實施細節。
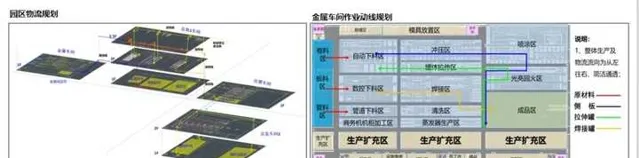
(6)針對具體作業進行流程升級和自動化改造設計,實作高效運轉。這是生產運作模式最佳化提升改善措施。
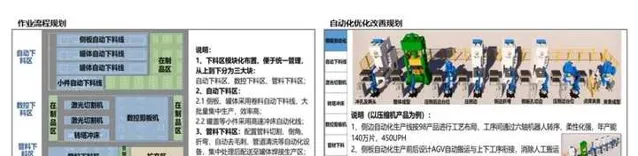
具體的精益實體流改善包含作業流程規劃、工時節拍、流程實施、人力規劃、8S和布局設計等內容,以上展示的僅是某客戶金屬制品部件做精益實體流時部份改善和最佳化方法,僅供參考。不同企業不同客戶,需要依據實際情況按需選擇和實施。
結語
結合企業戰略需求和未來業務規劃,透過智造資訊流和精益實體流「雙管齊下」 ,包含從生產模式、資源配套、業務流程、具體運作體系等內容,進行數位化轉型一體化從規劃到落地,實作企業業務飛速發展、高效執行、精細化管控、數位化提升的整體效果。